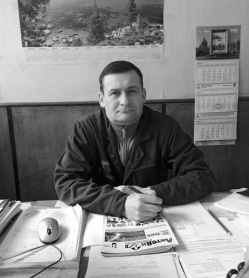
Как найти новую нишу
Алексей Юрьевич, расскажите о наиболее значимых этапах развития ОАО «Тяжпрессмаш».
У нашего предприятия - более чем полувековая история, оно хорошо известно в России и за рубежом. «Тяжпрессмаш» начинался как завод тяжелого машиностроения. В этой сфере было более 26 предприятий, сейчас по всей стране осталось всего несколько заводов. Если говорить о нашей области, то в советские годы в промзоне Рязани соседствовали три крупных предприятия: станкостроительный завод с 12 тысячами работников, предприятие по выпуску прицепного оборудования к комбайнам (около 10 тысяч) и завод тяжелого кузнечно-прессового оборудования «Тяжпрессмаш» — порядка пяти тысяч сотрудников. В 90-х годах прошлого века — начале 2000-х годов предприятия встали, тяжелое машиностроение потихоньку умирало. Сегодня нет в Рязани ни станкостроительного, ни комбайнового заводов. У нас работает 2500 человек, основная производственная площадка насчитывает 400 000 квадратных метров. Но самое главное - мы живы и развиваемся, за что огромное спасибо нашему руководителю Алексею Михайловичу Володину.
В кризисные годы важно было найти рынок, который бы позволил предприятию выжить. Когда произошел спад в отрасли тяжелого машиностроения, «Тяжпрессмаш» зашел в нефтянку. В то время в России в этой сфере рулили только иностранцы, именно они были королями всех заказов. Мы, имея мощную конструкторскую базу, купили несколько образцов зарубежной продукции для нефтегазового сектора, разобрали их, изучили. И наладили выпуск — можно сказать, импортозамещение. Со временем производство продукции для нефтяной и газовой промышленности стал одним из основных направлений «Тяжпрессмаша», сейчас это около половины объема всего производства завода.
В СССР было много проектных институтов, сейчас в их зданиях сплошные офисы. Выходит, больше некому проектировать прессы и станки?
Действительно, все проектные институты, которые создавали оплот и фундамент тяжелой промышленности, можно сказать, утратили свое значение. Теперь «Тяжпрессмаш» является единственным в России калькодержателем и хранителем чертежей прессов и тяжелых гидравлических в том числе, которые производились в советское время. Наши специалисты освоили выпуск комплексных линий «под ключ» - автоматических и полуавтоматических. Обслуживают комплекс пять человек, а производительность колоссальная. Китай очень заинтересован в таком оборудовании. Уже продали туда десяток автоматических линий по штамповке прутка. Они, конечно, пытались разобрать и сделать самим (Улыбается). После этого заказали еще несколько штук.
Не смогли продублировать?
А это не так просто, как кажется. Например, мы выпускаем такую известную вещь, как четырехбойковый ковочный блок. Это такой инструмент, который встраивается в обычный пресс и позволяет делать поковки круглого сечения с чистотой поверхности до 5 мм — практически один шаг до проката. Китайцы после покупки одного блока объявили, что сами будут выпускать любой типоразмер устройств. Но через год приехали и заключили договор еще на пять блоков. Это напоминает историю с автоматом Калашникова: выпускают все, а механизм все равно наш, российский.
Где найти штампы «Тяжпрессмаша»
Кто ваши основные потребители: отрасли и предприятия?
Завод продолжает выпуск специального кузнечно-прессового оборудования и осваивает изделия для смежных отраслей промышленности - автомобильной, авиационной, железнодорожной, нефтегазовой, атомной. Развиваем сотрудничество с Министерством обороны РФ - у предприятия есть лицензии на разработку, производство и утилизацию боеприпасов и их составных частей.
Пытаемся возродить металлургию. «Тяжпрессмаш» имеет возможность изготавливать практически любую продукцию металлургического производства. Среди основных потребителей - «ВолгаСтальПроект», ИП Кривицкий, «МетРесурс», ВТЦ «Тяжпрессмаш», «Оптима», «Металлоград», «Поковка», «ФерроБалт», «Фирма ЭПЛ», «ИнструментСервис», «СтальСистема», «ВЦОМ», «Эребус», «ПРОМГАРАНТ» и многие другие. Заказчики вроде бы не очень большие, но они в свою очередь поставляют продукцию на такие крупные предприятия как ГАЗ, КамАЗ. Так что на комплектующих, которыми пользуются отечественные гиганты машиностроения, стоят штампы из поковок и металла нашего предприятия.
Что представляет собой литейное производство «Тяжпрессмаша»? Какие технологии вы используете?
Раньше мы выпускали около 1200 тонн фасонного литья в месяц и 200 -300 тонн слитков, и все это шло на нужды тяжелого машиностроения. Сегодня это 150-200 тонн фасонного литья. Так как машиностроение сдвинулось к нулю, пришлось перенаправить силы и организовать выпуск собственных кузнечных слитков, увеличив их выпуск до 1500-2000 тонн в месяц. Модернизировали нашу старую кузницу: было два пресса мощностью по 2000 тонн, увеличили до 2500 тонн, сами спроектировали слитки и оснастку. Отработали металлургическую технологию по производству стали, освоили более 150 марок стали — это и подшипниковые ШХ-15, и холоднорежущие 9Х1 и нержавеющие для нефтегазовой отрасли. Для сравнения: 15 лет назад выпускали всего 18 марок, причем все они были простыми.
В дуговых сталеплавильных печах типа ДС-6Н1 емкостью 6 тонн и ДППТУ-20 емкостью 20 тонн производится выплавка металла для станин, корпусов, барабанов, колес, блоков, плит и других деталей развесом от 15 килограммов до 15 тонн. Печь для плавки цветных сплавов ДМК-0,5 позволяет выплавлять методом фасонного литья заготовки с максимальными размерами 1000х300х50 мм, болванки диаметром от 40 до 200 мм и весом от 5 до 500 кг. Производим кузнечные слитки весом от 0,75 до 17 тонн.
На тяжелых гидропрессах и молотах изготавливаются поковки прямоугольного, круглого сечения, сплошные и пустотелые диски, бруски, штоки, плунжеры, поковки раскатных колец, бандажей. Можем провести испытания поковок на механические свойства, УЗК по ГОСТ 24507-80 и другим стандартам. А использование на прессах четырехбойкового ковочного устройства позволяет осуществлять радиальную ковку слитков и заготовок.
Что считается визитной карточкой вашего предприятия? Расскажите об уникальных заказах и продукции.
Последние семь-восемь лет вплотную занимаемся литьем по газифицированным моделям. «Тяжпрессмаш» является основным поставщиком московского «Водоканала». Отгружаем в столицу опорно-укрывные элементы: затворы щитовые стандартные диаметром перекрываемого канала от 600 до 3500 мм, затворы щитовые овальные, плоские, поворотные, штанги, гидравлические хомуты и муфты, решетки механические сорозадерживающие. Опорно-укрывные смотровые элементы стали визитной карточкой - на Красной площади лежат люки производства «Тяжпрессмаша». Десятки тысяч единиц продукции используются по всей России. В шутку говорим: « За водой и движением отходов под Москвой приглядываем мы».
Щитовые системы для канализационных стоков раньше выпускали немцы, но сегодня весь заказ выполняет наше предприятие. Это именно то, что нам позволяет жить — здесь чуть-чуть, там чуть-чуть, с каждой сферы происходит подпитка, и наше предприятие продолжает устойчиво работать и развиваться.
Еще один постоянный заказчик предприятия — компания «Турбохолод». Мы поставляем ей турбодетандеры — устройства, через которые перекачивают газ из земли в магистраль. Зимой на улице атмосфера минус 60, а под землей плюс 110 — и в таких сложных условиях оборудование должно бесперебойно работать. Поэтому мы делаем такое оборудование из стали 09Г2С и только из своего металла, а «Турбохолод» устанавливает в них турбины. Лет десять назад такую продукцию выпускали только иностранцы, сегодня мы практически единственные на российском рынке, кто может это сделать.
Ну и, конечно, тот самый четырехбойковый ковочный блок, тяжелые прессы и штамповочные линии, о которых мы говорили выше. Все это тоже наши визитные карточки!
Дорогу осилит идущий
Сколько продукции производите для российских заказчиков и на экспорт?
На экспорт идет 10 – 15 процентов от всего объема. В основном это поковки прямоугольного и круглого сечений с проверкой ультразвуковым контролем. Больше ориентированы на внутренний рынок бывшего СССР.
В этом году предприятию «Тяжпрессмаш» исполняется 65 лет. Как обстоят дела с модернизацией?
Производственные мощности завода состоят из тесно взаимодействующих между собой технологических производств: металлургическое, термическое, сварочное, механосборочное, производство лакокрасочных покрытий, гальванических покрытий, резинотехнических изделий и пластмассы.
В 2018 году на ВДНХ получили золотую медаль за инновации в машиностроении — сами спроектировали, изготовили машину центробежного литья грузоподъемностью 25 тонн модели РМЦ-1000. Собираемся двигаться в сторону теплотехники.
Что касается мощностей по фасонному литью, то они, конечно, устарели — есть смесители 50-х годов. Планируем в 2020-2021 годах осуществить техническое перевооружение сталелитейного цеха. Сейчас мы закупаем новый смеситель непрерывного действия производительностью 25 тонн в час. Поставили фундамент — запускаем его в конце апреля этого года. Выиграли федеральный грант и модернизируем шеститонную дуговую печь - переводим трехфазную дуговую электропечь на постоянный ток и работу по типу два сводовых электрода без подовых. До конца года печь однозначно будет работать. В планах - приобретение нового термического оборудования. Так получилось, что наше предприятие испытало продукцию всех производителей печей постоянного тока — и «ЭКТа», и «Толедо», пришел черед «ФЕРРОМСТАЛЬ».
Какова динамика объемов производства за последние годы?
Если рассматривать показатели в рублях, то растет, если в тоннах, то снижается. Каждый год падение на пять-семь процентов. Думаю, что это общая картина не только для отрасли машиностроения или металлургии, а вообще для всех промышленных предприятий.
Что касается потребностей «Тяжпрессмаша» в чугунных и стальных заготовках, то до 2022 года закроем их собственной производственной базой.
Несмотря на кризисную ситуацию наше предприятие отстаивает свою нишу и борется за место под солнцем. Заказчики к нам едут со всей страны — даже с металлургического, казалось бы, Урала.
Дорогу осилит идущий. Конечно, у любого предприятия сейчас есть падение, мы тоже в тяжелой ситуации. Тем не менее покупаем новый плавильный агрегат, который в общей сумме, думаю, обойдется предприятию в 100 миллионов рублей, а лишних денег, как вы понимаете, никогда нет. Весь капитал исключительно из нашей прибыли. Как нам говорят: поэтому вы и живы, что у вас весь капитал внутри предприятия. А так распилили бы на кусочки, как и многих, и пустили под склады.
Какие проблемы отрасли актуальны для вашего предприятия? Что должны предпринять власти для их решения?
Убежден, что такие отрасли, как металлургия и машиностроение, должны иметь доступ к льготному финансированию. Это позволит предприятиям своевременно переоснащаться, решать вопросы по качеству выпускаемой продукции. Нам на некоторые станки приходится тратить годы — не так просто выделить деньги из бюджета. А при льготном кредитовании мы бы уже давно закупили все самое передовое. Конечно, существуют различные фонды поддержки промышленности, но при работе с ними возникает очень много подводных камней.
«Всегда работал с металлом»
Алексей Юрьевич, как давно вы в металлургии, кем работали и когда пришли на завод в Рязани?
Родился в Алмалыке, окончил Ташкентский государственный технический университет, получил специальность инженера-металлурга. Начинал плавильщиком на печи кислородно взвешенной плавки (КВП) на медеплавильном заводе в Алмалыке в системе АГМК. Далее работал начальником производства в институте «УзНИПРОЦВЕТМЕТ», потом перешел начальником производства на совместное узбекско-израильское предприятие «УзМетал Технолоджи». В 2004 году судьба перебросила в Россию, пришел на ОАО «Тяжпрессмаш» инженером-технологом отдела главного металлурга. Через полгода стал начальником металлургического бюро отдела главного металлурга, в 2007 году назначен заместителем главного металлурга. В общем, всегда работал с металлом.
Считаю, что за последние годы наше предприятие здорово продвинулось в металлургическом направлении. Освоили больше ста марок стали, причем, не только по количеству, но и по качеству. Самое интересное — половина нашей продукции, будь то пресс или манипулятор, производится из нашего же металла. То есть мы закупаем электронику, а для остального применяем свои металл и заготовки. Это позволяет, во-первых, задействовать потенциал персонала предприятия, а, во-вторых, гарантировать необходимые эксплуатационные характеристики для нашего оборудования. Мы уверены в своем металле и можем отвечать за надежность продукции.
Блиц-интервью
Производство или офис: где проще?
Офисным работником не был. В производстве, думаю, проще, там все более-менее ясно, есть задача и план. Допустим условно назовем ОГМет офисом все не просто. От каждого твоего решения зависит результат в производстве и решения принимаются далеко не простые и очевидно эффективные, что приводит порой к трениям с производственниками. Но рано или поздно находится компромисс.
Будущее литейной отрасли в трех словах.
Оно, можно сказать, туманно. Задачи все сложнее, требования к продукции все выше. Но несмотря на трудности считаю, что дорогу осилит идущий.
Чем увлекаетесь в свободное время?
Рыбалка по возможности, настольный теннис, прогулки на велосипедах с семьей. Любим семьей ходить в кино.
Анна Литовина.
Фото ОАО «Тяжпрессмаш».