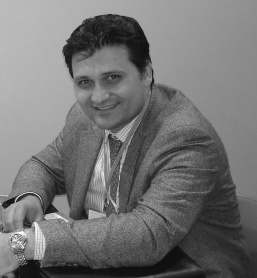
Как адаптироваться к новым требованиям, потенциал какого литья пока недооценен, в чем преимущества автоматической формовочной линии, легко ли работать с историческим наследием и почему не надо опасаться новомодных принтеров? Об этом и о многом другом мы беседуем с членом совета директоров компании «МеталЛитМаш» Джузеппе Маццарелли.
Вдогонку за конструкторами
Компания «МеталЛитМаш» создана на базе металлургического производства бывшего завода ПО «Коломенский завод тяжелых станков». Давайте сравним стартовые позиции и уровень, которого компания достигла за 18 лет.
В 2000 году мы купили на аукционе цеха бывшего завода ПО «Коломенский завод тяжелых станков». Предприятие заинтересовало расположением недалеко от Москвы, цеха были не совсем убитые - мостовые краны еще двигались, трансформаторы работали. Сохранился костяк коллектива — человек 40. Завод был частично арендован, но все шло к закрытию. Начали возрождать предприятие, хотя тоже не без приключений. Как говорил великий Черномырдин, хотели как лучше, а получилось, как всегда (Улыбается). То, что мы планировали сделать за два-три года, осуществлялось намного дольше. Через четыре месяца завод объявили банкротом, прошла цепочка разных управляющих. Все эти процессы закончились только в 2005-06 годах. Тут же мы начали ставить новое оборудование. Сначала автоматическую линию, смесе-приготовительное отделение, потом заменили очистное оборудование, установили допоборудование по ХТС, по стержневым машинам. В общем, дело сдвинулось.
Сейчас на предприятии трудятся 250 человек работает. Основным является цех мелкого и среднего литья. Выпускаем около 700 тонн литья в месяц — высокопрочный чугун разных марок с шаровидным графитом и серый чугун.
В советские времена основная нагрузка приходилась на цех крупного и тяжелого литья. Какова его судьба?
Цех крупного и тяжелого литья в свое время выпускал до 30 тысяч тонн литья в год. Когда спрос упал, цех закрыли. Это было в 1996 году, еще до нас. Наверняка закрыли бы и цех мелко-среднего литья, его тогда довели до смешных 30-40 тонн в месяц. Сейчас разрабатываем проект реконструкции цеха крупного литья. В будущем планируем делать отливки весом до 75 тонн.
Потребители из каких отраслей — ваши клиенты?
Плотно работаем с железнодорожниками — Тихвинский вагоностроительный завод, ряд других предприятий, выпускающих, например, тормозные системы. Среди наших клиентов — представители тяжелого машиностроения, энергомашиностроения, производители автокомплектующих. Основной упор делаем на мелкое и среднее литье развесом до 120 кг. В данном сегменте у нас есть определенное преимущество, потому что мы установили автоматическую формовочную линию. Она дает стабильные показатели по геометрическим размерам, можем выполнять массовые серии.
Насколько капризны заказчики? Как менялись их требования за минувшие годы?
Требования бурно и стремительно меняются с каждым годом. И все это вызвано той самой конкуренцией. Разработчики совершенствуют машины, придумывают, как сделать свой механизм более эффективным. Соответственно, применяют решения по удешевлению либо снижению веса, что приводит к большим проблемам для литейщиков. Нужно использовать другие марки материалов, более легкие и одновременно прочные детали. Все это повышает технологическую нагрузку. Конструктора не хотят отставать от своих коллег, поэтому каждый год часть своей боли они выливают на нас. Например, один заказчик деталей начал с требований простого ВЧ-50, а потом за два года исходный материал превратился в ВЧ-70. При этом с относительным удлинением не меньше 4-5%, определенной структурой по матрице и процентным составляющим шаровидного графита. То есть фактически перешли с общепотребляемого на очень специфичный, сверхпрочный материал.
Почему сложно адаптироваться? Потому что часто заказчики приходят с очень сжатыми сроками. Нужно иметь достаточно хороший ресурс с точки зрения технологий, своевременного изготовления оснастки и короткий цикл от рисования до исполнения и выдачи первых образцов заказчику, чтобы тот мог принять решение — покупать или нет
Искусство адаптироваться
На что мотивирует сегодняшняя экономическая ситуация в России?
Ужесточились требования к отливкам. Но мы нашли постоянный спрос в том, что раньше импортировались. Когда доллар стоил 30-35 рублей, евро 40-45 рублей, то платить, скажем, 2,5-3 доллара или до 4 евро за килограмм никто не хотел. Это были большие деньги. Падение рубля изменило расклад сил. Те предприятия, которые могут сделать качественное литье, равноценное импортному, сегодня работают стабильно. А те, кто по ряду причин — устаревшее оборудование, неадекватные технологии и так далее — уступает в качестве, стали заложниками канализационного, строительного, декоративного и садово-паркового литья. На эту продукцию спрос то есть, то нет.
В общем выход один - обновляться, оптимизироваться и выходить на более высокий уровень качества. Если корпорациям нужно литье, оно будет закупаться. Другой вопрос — где, как и за какую цену. По статистике, ежегодно Россия расходует примерно два миллиона автомобилей, 400 тысяч единиц транспорта и тяжелой техники и около 100 тысяч машин перемещения грунта — тракторов, грейдеров и так далее. Все производители при таких объемах пытаются локализовать свое производство, а это в первую очередь штамповки, поковка, сварка и литье. Так что рынок есть. С жесткими требованиями, под которые надо подстраиваться.
В чем, на ваш взгляд, уникальность производства «МеталЛитМаш»?
Мы добились определенного успеха — сумели сохранить и расширить технологическую базу, а также человеческий потенциал. Чтобы получить годную деталь, нужно правильно составить технологию. А это сложный процесс: есть заводы, попадающие с первого-второго раза, а есть те, кто и с десятого раза в техусловия не попадает. Мы относимся к первой категории. Несмотря на сложность задач, а у нас больше 80 разных заказчиков и более 1000 единиц в номенклатуре производства, мы быстро переходим с одной оснастки на другую, с одного заказа на другой. Если необходимо закупить эффективное оборудование, которое позволит удерживать баланс между ценой и качеством, то это делается. Мы переоснащаемся, добавляем единицы, реконструируемся. Можно ли это назвать уникальностью? Скорее это конкурентное преимущество, которое позволяет удерживать заказчика в непростых условиях и развивать предприятие.
Расскажите о программе дальнейшего развития завода.
Жизнь заставляет каждое заготовительное производство, будь то литейное, кузнечно-прессовое, сварочное и так далее, давать заказчикам готовую либо полуготовую продукцию. Поэтому мы развиваемся многогранно. Первым делом вкладываемся в мехобработку, чтобы дать клиенту не просто заготовку, которую он должен обрабатывать и собирать в узел, а уже готовый продукт или деталь.
Второе направление — оптимизация литейного производства. Оборудование работает в условиях износа, температуры и так далее. Есть агрегаты, которые уже свое отработали, их нужно заменить. Поэтому каждый год закупаем и внедряем новое оборудование - очистное, автоматизированные комплексы, заливочные машины, которые позволяют быстрее заливать формы. Конечно, все купить и заменить невозможно, слишком большие затраты. Стараемся придерживаться графика поэтапной замены.
Третье направление — развитие крупного и тяжелого литья. Сегодня предприятий, которые могут отлить заготовку весом более 15-20 тонн, в стране осталось немного. Это Петрозаводск и ремонтные цеха больших металлургических предприятий. Правда, последние не привыкли работать по требованиям станкостроения. Мы видим очень большой потенциал у цеха крупного и тяжелого литья. Естественно, мы не спешим развивать тот объект, пока мы здесь не достигли комфортного уровня автоматизации и производительности. Сейчас мы на этапе проектов.
Отливали Москву
На вашем заводе производили литье для реконструкции центра Москвы. Получается, вам столица обязана своим новым обликом?
Мы делали много литья для Москвы, но никогда не выступали первым лицом. Поэтому наше предприятие фигурирует только в проектной документации и отчетах правительства Москвы. Мы поставляли продукцию фирмам, которые механически обрабатывали литье, красили и устанавливали. Например, мы отлили все чугунное литье на Патриарших прудах, за исключением бронзовой скульптуры Рукавишникова, — все заборы, ограды, скамейки, фонари. Отливали литье для сквера на Садово-Кудринской улице, на Знаменке два объекта — около Генштаба и Военной академии имени Фрунзе, часть Александровского сада около могилы Неизвестного солдата, в том числе красивые чугунные урны.
Какой объект запомнился больше всего?
Самой сложной и трудоемкой работой стала винтовая лестница на колокольне Ивана Великого в Кремле. Заказчик предполагал, что будет всего пять видов ступеней на всю лестницу. Мол, аккуратненько вынем и принесем литейщикам. Но когда начали работать, столкнулись с неожиданной ситуацией. Вынуть ничего нельзя, потому что все превратилось в труху и грозит рассыпаться из-за неосорожных движений. Камни самые разные, из-за ограничений архнадзора каждая ступенька была разного размера. Мы даже посылали туда своих модельщиков. По лекалам и шаблонам они отмечали, каким образом перерабатывать модельную оснастку, чтобы начать с самой большой ступеньки и постепенно пилить ее до минимальной. К тому же там пропускной режим, масса ограничений. И мы все дружно с ума сходили от этой лестницы. Просто кино! Эта сложная задача запомнилась на всю жизнь.
Брак заставил пойти в производство
Джузеппе, у вас не самые типичные для России имя и фамилия. Откуда вы родом?
Можно сказать, я - продукт студенческого обмена (Улыбается). Папа у меня итальянец, мама русская. После того, как окончил университет в 1994 году, большую часть времени провожу в России. А с 2001 года, когда занялся литейным производством, вообще надолго не покидал страну. Сами понимаете, литейное производство требует постоянного внимания.
Но поначалу вы были далеки от литейщиков.
Предыдущее поколение моей семьи вело торговлю с Россией. Поставляли различное оборудование: канато-вязальное, сетевязальное, все, что требовалось в разных отраслях Советского Союза. Потом времена изменились: не стало плановой экономики, внешней торговли, СССР ушел в прошлое. Мы начали искать, что можно экспортировать из России в Италию и страны Европы. После долгого и мучительного периода сосредоточились на литье и штамповке. Я ездил по многим заводам, размещал заказы от итальянской, немецкой и прочей европейской промышленности.
Почему решили вложиться в производство?
В 90-е годы прошлого века сложилась ситуация, когда многие заводы работали на износ. У них не было денег на обновление, на новые технологии. Постепенно уровень брака у наших поставщиков вырос настолько, что мы поняли: либо по-другому подходим к делу, либо выходим из этого бизнеса. Сначала была идея создавать совместные предприятия, но по ряду причин это не получались. Тогда учредители приняли решение организовать производство, которое соответствовало бы требованиям иностранных заказчиков — итальянцев, немцев, французов. Начали искать, где разместить производство. Выбор пал на Коломну.
В итоге ваша жизнь крепко связана с литейной промышленностью. Насколько это вам близко и интересно?
Литейное производство интересно тем, что заказчики и их требования самые разные. Имея дело с представителями той или иной отрасли, понимаешь проблематику, просчитываешь заранее, что каждому из них нужно. Часто бывает так: приходит новый заказчик, набрал сундук терпения. А мы сразу перечисляем, что и когда нужно обеспечить. Потому что уже знаем специфику его отрасли или рынка.
В мехобработке я видел множество печальных примеров, когда целые пролеты станков предыдущего поколения вывозились в металлолом. Потому что появлялись современные станки с ЧПУ. В литейном производстве такого нет. Одно время говорили, что новомодные принтеры уничтожат все литейки. Но ничего подобного не случилось. Потому что себестоимость деталей, сделанных принтером, в десятки, если не в сотни раз дороже, а их производительность, не идет ни в какое сравнение. Если мы в месяц можем делать десятки тысяч деталей, то принтер — одну/две в день. Мы углубляемся в проблемы многих видов промышленности, это всесторонне обогащает. Так что не жалею, что попал в литейщики.
Блиц-тайм
1. Революция или эволюция?
Мне ближе эволюция. За 18 лет — а первая плавка у нас была в феврале 2001 года — все, что мы делали эволюционным образом, получалось. Сразу или попозже. А то, что пытались сделать революционным наскоком, обычно имело плачевный исход.
2. Свободное время и увлечения.
Свободное время отдаю прежде всего семье и детям. У меня мальчик и девочка, им 13 и 10 лет. Старший играет в футбол и занимается плаванием, многогранный атлет, то и дело вызывает меня на соревнования. Младшая плавает и бегает. Сам тоже стараюсь следить за здоровьем, четыре-пять раз в неделю хожу в спортзал.
3. Мечта и реальность. Каково соотношение в вашей жизни?
Сложный вопрос — всегда хочется большего. Для меня актуальнее соотношение «ожидание - результат». Ожидание обычно превышает результат, но изредка результат догоняет ожидания. Получается счастливый случай!
Анна Литовина
Фото: «МеталЛитМаш»